The Role of Hard Alloy Tungsten Ball Seats in High-Pressure Valve Performance
- xiongchengcemented
- May 8
- 5 min read
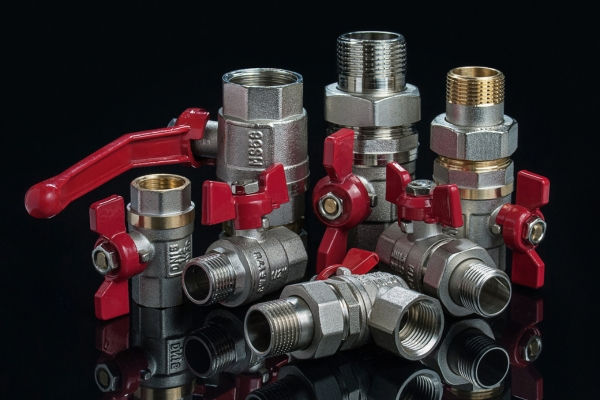
High-pressure valves are critical components in various industrial applications such as oil and gas, chemical processing, aerospace, and power generation. These valves are designed to regulate, control, and direct the flow of liquids or gases under high pressure. The performance and reliability of these valves are paramount, as any failure can lead to safety hazards, operational shutdowns, or substantial financial loss. The ball seat plays a particularly crucial role among the many components that determine a valve's efficiency. Increasingly, manufacturers are turning to hard alloy tungsten steel ball valve ball seats to meet the stringent demands of modern high-pressure systems.
Understanding Ball Valve Design
Ball valves are named for the spherical disc—the ball—that controls flow through it. When the valve is open, the ball's hole aligns with the flow path, allowing fluid to pass. When closed, the solid part of the ball blocks the path. The ball seat is the part the ball rests against when the valve is closed. This seat must maintain a secure seal to prevent leaks, even under extremely high pressures and temperatures. Therefore, the choice of material for the ball seat directly impacts the valve's sealing ability, durability, and overall performance.
Why Material Selection Matters
Materials face extreme mechanical stress, potential corrosion, and significant wear and tear in high-pressure environments. Conventional materials like plastics or soft metals often fail to provide long-term reliability under such conditions. This is where hard alloys, especially tungsten-based ones, come into play. A hard alloy tungsten steel ball valve ball seat offers superior hardness, wear resistance, and thermal stability, making it ideal for challenging industrial conditions.
Properties of Tungsten Alloys
Tungsten, known for its high melting point and incredible hardness, becomes even more resilient when alloyed with steel or other metals. This combination yields materials that can withstand high compressive forces, resist deformation, and maintain their integrity in corrosive and high-temperature environments. These characteristics make hard alloy tungsten steel ball valve ball seats highly desirable in systems where reliability and precision sealing are non-negotiable.
Enhanced Sealing Performance
A primary function of any ball seat is to ensure a leak-proof seal when the valve is closed. In high-pressure applications, achieving this is no simple task. Fluids at high pressure can force their way through minute gaps or imperfections in the seat surface. The exceptional hardness and dimensional stability of hard alloy tungsten steel ball valve ball seats ensure that the ball maintains consistent contact with the seat, preventing leaks. Their ability to resist indentation and maintain a tight seal even under repeated opening and closing cycles adds to the valve’s reliability and lifespan.
Wear Resistance for Longevity
Valves in high-pressure systems are often subjected to continuous use. Repeated operation can lead to surface wear, eventually compromising the valve's ability to seal. A hard alloy tungsten steel ball valve ball seat provides outstanding wear resistance, even in abrasive flow conditions. Whether the valve handles slurry, high-velocity gas, or corrosive chemicals, the seat remains intact far longer than softer materials. This extended service life reduces maintenance needs, minimizes downtime, and lowers the total cost of ownership for the system.
Thermal Stability Under Extreme Conditions
Industrial systems often expose valves to extreme temperatures, especially when dealing with steam, superheated gases, or chemical reactions. A ball seat material must retain its structural integrity and performance characteristics even at high temperatures. Hard alloy tungsten steel ball valve ball seats excel in this area, offering excellent thermal stability that prevents softening, expansion, or other forms of thermal degradation. This capability is particularly valuable in power plants, petrochemical refineries, and other high-heat environments.
Corrosion Resistance
Corrosive fluids such as acids, bases, or seawater can quickly degrade standard valve components. Tungsten alloys are highly corrosion-resistant, especially compared to conventional steel or polymer-based seats. This resistance ensures that the valve continues to operate efficiently and safely even in chemically aggressive environments. As a result, hard alloy tungsten steel ball valve ball seats are commonly used in offshore drilling rigs, chemical plants, and desalination facilities.
High Pressure Endurance
Pressure ratings are a key consideration in valve selection. As system pressure increases, the load on valve components multiplies, often pushing materials to their limits. The strength and rigidity of tungsten alloy make it an ideal candidate for handling these extreme conditions. Unlike softer metals that may deform or crack under high loads, hard alloy tungsten steel ball valve ball seats retain their shape and functionality, ensuring continuous operation under even the most demanding conditions.
Precision Engineering and Surface Finish
To ensure a reliable seal, the ball and seat must mate perfectly. This calls for a high degree of precision in manufacturing and an excellent surface finish. Tungsten alloy materials lend themselves well to precision machining and polishing techniques. The result is a seat with minimal surface imperfections, which enhances contact with the ball and contributes to superior sealing performance. In high-precision industries, such as aerospace and medical equipment manufacturing, this level of quality can be the difference between success and failure.
Compatibility with Advanced Valve Designs
Modern engineering demands components that perform well and integrate seamlessly into complex systems. Hard alloy tungsten steel ball valve ball seats are compatible with various advanced valve configurations, including trunnion-mounted and floating ball valves. Their ability to handle both unidirectional and bidirectional flow systems makes them a flexible choice for engineers designing sophisticated fluid control systems. Moreover, these seats can be customized to specific dimensional and performance requirements, providing a tailored solution for diverse industrial needs.
Lower Maintenance Requirements
Downtime for maintenance and repairs is costly in industrial settings. Components that require frequent replacement or adjustment can significantly affect operational efficiency. Thanks to their durability and resistance to wear and corrosion, hard alloy tungsten steel ball valve ball seats require less frequent maintenance. Their long service life also means that scheduled maintenance intervals can be extended, resulting in increased productivity and lower operating costs.
Environmental and Safety Benefits
Leaks and failures in high-pressure valves can lead to environmental contamination and pose serious safety risks. A reliable seal provided by a tungsten alloy ball seat minimizes the risk of leaks, enhancing the system's overall safety. Additionally, the reduced need for maintenance and replacement means fewer resources are consumed over the valve's lifetime, contributing to more sustainable industrial practices.
Economic Advantages Over Time
While hard alloy tungsten steel ball valve ball seats may have a higher initial cost than seats made from conventional materials, their long-term economic benefits are significant. Their extended service life, reduced downtime, lower maintenance requirements, and improved system reliability all contribute to a lower total cost of ownership. For industries that operate 24/7 and cannot afford frequent shutdowns, this makes tungsten alloy seats a sound investment.
Supporting Industry Innovation
As industries evolve, the demand for more efficient, reliable, and high-performance components grows. Hard alloy tungsten steel ball valve ball seats support this innovation by enabling valves to operate effectively under extreme conditions. Their use paves the way for new engineering possibilities, allowing for developing more compact, efficient, and high-capacity systems. These ball seats are foundational in pushing industrial capabilities forward, from deep-sea drilling operations to space exploration technologies.
Future Prospects and Advancements
Material science continues to advance, and new manufacturing techniques are enhancing the performance characteristics of tungsten alloys. Future developments may include composite materials that further improve corrosion resistance, or coatings that reduce friction and enhance sealing capabilities. As the global industry becomes more focused on efficiency and sustainability, the role of hard alloy tungsten steel ball valve ball seats will likely become even more prominent.
Conclusion
In the world of high-pressure fluid systems, performance, reliability, and safety are non-negotiable. The hard alloy tungsten steel ball valve ball seat has proven vital in achieving these goals. Its exceptional wear resistance, thermal stability, sealing capability, and corrosion resistance make it a top choice for demanding industrial applications. As technology progresses and the demands on industrial systems increase, these ball seats will continue to play an essential role in ensuring that high-pressure valves perform at their best.
Comments